根據 Automotive News Europe 報導,鑒於碳纖維高昂的成本,BMW 為了維持一定的利潤水準,正在縮限碳纖維的使用量,並將輕量化的目標轉移至其他材質,例如鋁合金以及高強度鋼材等。
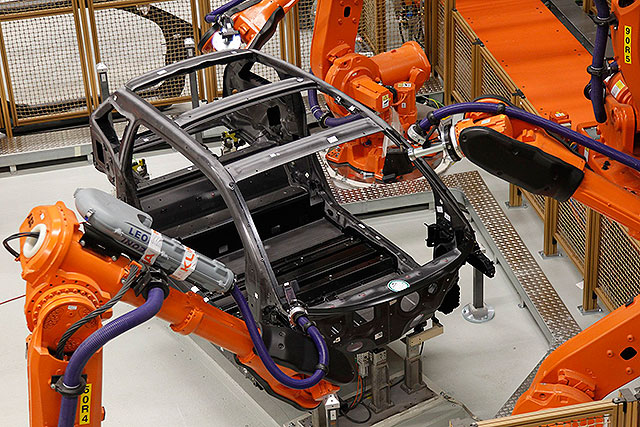
其實 U-CAR 在今年 8 月就報導過下一代 i3 可能會取消全碳纖維車體的設計,而改採鋁合金、或是使用現行 7 Series 的 Carbon Core 鋼碳複合結構,不難看出碳纖維的成本問題的確讓 BMW 不得不開始尋找替代方案。
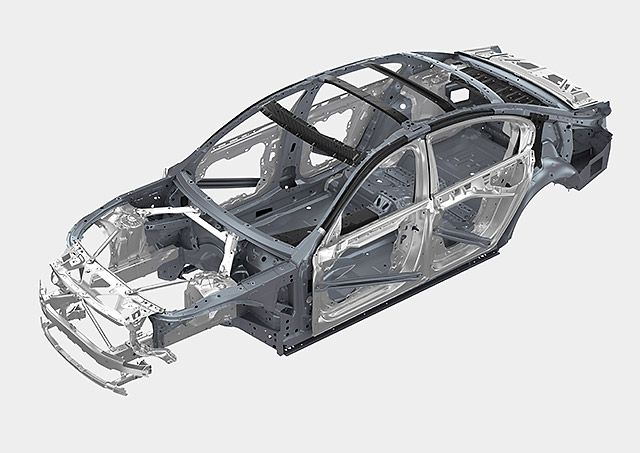
BMW 擘劃 i 電動車藍圖,企圖心強但也耗費龐大資源
Oliver Zipse重點在於 BMW 願意花多少成本來減輕 1 公斤,不是單純討論單一材料就好,而是要思考如何結合碳纖維以及各種材料。 Oliver Zipse, BMW 生產總監
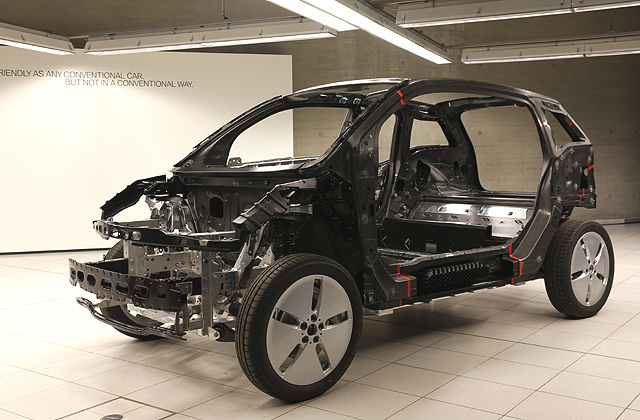
2013 年發表的 i3 使用大量的碳纖維部件,而碳纖維的成本每公斤約 16 歐元(約台幣 567 元),相比之下鋼材每公斤成本不到 1 歐元(約台幣 35 元)。高昂的成本造就 4.5 萬歐元(約台幣 160 萬元)的售價,結果銷售表現並不亮眼。
(編按:原文中誤將鋼材成本誤植為鋁合金,感謝網友指正)
銷售數據是最好的說明,在 BMW 原廠於 2013 年底以 i3 為主力,推出集團電動車 i 子品牌以來,至 2016 年全球市場 i 品牌電動車累積銷售量達到 10 萬輛,某一層面,這項成績單對於傳統車廠而言,其實已經是少有對手能夠比擬,但相較於龐大的研發投資,以及自行建立碳纖維車體生產體系的大膽策略,3 年 10 萬輛的銷售成績,仍讓 BMW 對於電動車的進展感到無比壓力;尤其,對比正在預購當中的 Tesla Model 3,售價 3.5 萬美元 (約台幣 110.8 萬元),還沒上市開賣,就已經收到 40 萬張預購單。
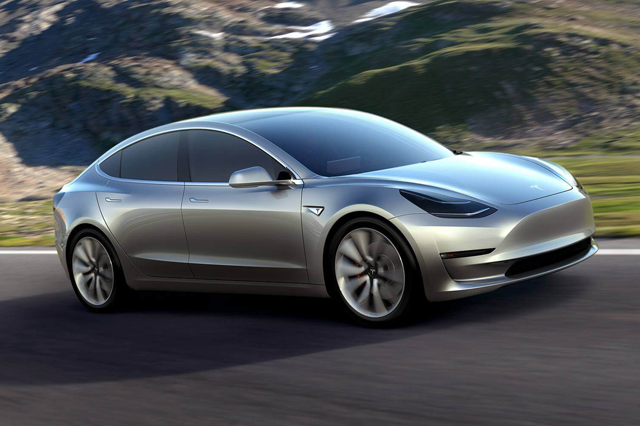
而之所以原本採用全碳纖維車體並不是沒有原因,因為對電動車而言,最大的成本其實在於電池,而越輕的車體、需要的電池越小,在無法改變電池成本的前提下,才會開發全碳纖維車體。不過隨著科技進步,從 2013 年至今電池效率已經提升 50%,讓 BMW 開始重新思考碳纖維的用量。
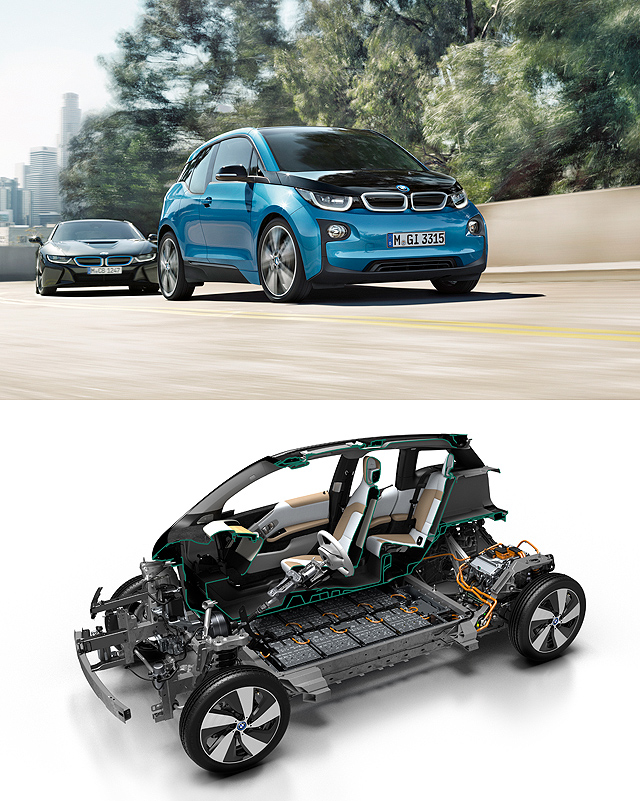
Harald Krueger大量使用碳纖維,對於較小級距的車輛而言成本太高,將導致產品失去競爭力。Harald Krueger, BMW CEO
根據 Harald 的說法,短時間內應該不會再看到 BMW 旗下車款採用全碳纖維車體,甚至 Carbon Core 車體技術也只會應用在高利潤的 7 Series,其他車系也將無緣搭載。不過投資超過 6 億歐元在碳纖維技術上的 BMW,仍然與對手例如 Mercedes-Benz 或是 Audi 有一定的差距,目前 BMW 將會把主力放在開發更多類似 Carbon Core 車體的複合結構技術。
討論區
成為第一個發表的人